Basics of electrospinning
Electrospinning is a fascinating technique for making continuous and very thin fibers from a variety of polymers and it even allows the incorporation of non-polymeric materials in the fiber cores. Over the last few years it has rapidly been gaining in attention, much due to its ability to produce fibers of exceptionally small diameter—down to a few nanometers [1]. In contrast to conventional spinning, the process is not driven by the pressure applied to the spinning solution, which actually flows quite slowly through the spinneret. Instead, a high voltage is applied between the spinneret and the spinning target (the collector), leading to separation (and possibly generation) of ions within the spinning fluid. The resulting electrostatic forces are eventually sufficiently strong that they overcome the surface tension of the fluid, resulting in a thin jet being ejected from the droplet that protrudes from the spinneret. Because this jet is highly charged, with a charge density that continuously increases due to evaporation of the solvent, it experiences bending instabilities induced by electrostatic self repulsion. This gives the jet a spiraling whipping motion that extends its effective path by orders of magnitude compared to the small distance between spinneret and collector. The lengthening leads to a dramatic thinning of the fiber and this is the reason for the exceptionally thin fiber diameters that may result from electrospinning.
The jet does not break up into droplets, as is the case in the related process of Electrospray, thanks to the dissolved polymer. This must be of sufficient size and its concentration must be high enough to counteract the Rayleigh instability, keeping the jet intact. The basic physics is the same (although the electric field in our case complicates things a bit) as that which keeps the water jets of fire fighters intact over much longer distances than would be possible with pure water, allowing them to put out fire even in rather high buildings; the water they use contains a small amount of high molar mass water soluble polymer.
A detailed introduction to electrospinning, focused on the type of work done in the ESMP group, can be found in Jan's habilitation thesis.
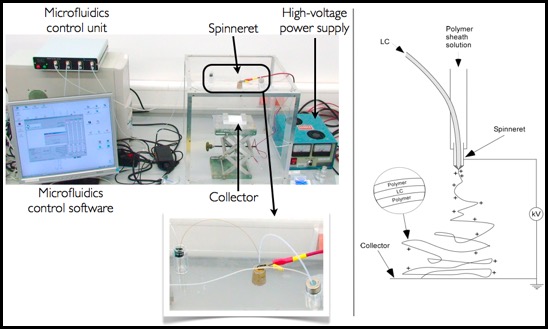
Our lab set-up for coaxial electrospinning of liquid crystal-functionalized polymer fibers (left) and a schematic drawing of the spinning process (right).
Coaxial electrospinning
We work mainly with coaxial electrospining [2], in which one fluid is spun inside another. This is achieved by inserting a thin flexible capillary into the tube through which the main spinning solution is pumped. The capillary, through which the inner fluid is pumped, is positioned such that it runs coaxially inside the spinneret and ends at the same point. In our case the inner fluid is often a liquid crystal and the outer is a water- or ethanol-based polymer solution. The end result is a fiber with core-sheath geometry, where the sheath is a solid polymer and the core is a liquid crystal (still in a fluid state), colloid or another functional material.
Fibers with liquid crystal in the core
Liquid crystals are ordered, anisotropic fluids, with many unique functionalities. These may be transferred to the fiber containing the liquid crystal, as shown in the example below. The liquid crystal is in this case a chiral nematic (also called cholesteric) phase with a helical modulation of the direction of ordering. The periodicity of the helix is in the range of optical wavelengths and this leads to Bragg reflection of a specific wavelength. This is why the fibers appear strongly green on the black background.
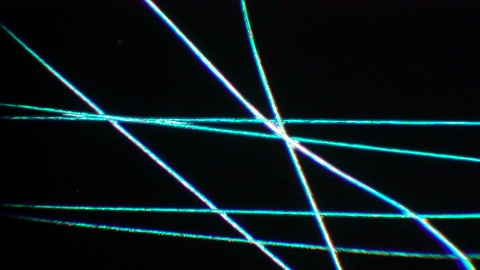
PVP fibers containing a short-pitch cholesteric liquid crystal shine brightly green when observed in a polarizing microscope. The selectively reflected color depends on the structure of the liquid crystal and since this is very sensitive to external influences, the fibers could be used in different types of sensors.
We have electrospun fibers with several other liquid crystal phases as well, as you can read in the following papers:
- Coaxial electrospinning of microfibres with liquid crystal in the core
J.P.F. Lagerwall, J.T. McCann, E. Formo, G. Scalia, and Y. Xia
Chem. Commun., 42, pp. 5420-5422 (2008) - Electrospun microfibres with temperature sensitive iridescence from encapsulated cholesteric liquid crystal
Highlighted on the journal cover page
Eva Enz and Jan Lagerwall
J. Mater. Chem., 20, 33, pp. 6866-6872 (2010) - Liquid Crystals in Novel Geometries prepared by Microfluidics and Electrospinning
Hsin-Ling Liang, Eva Enz, Giusy Scalia and Jan Lagerwall
Mol. Cryst. Liq. Cryst., 549, pp. 69-77 (2011) - Coaxial electrospinning of liquid crystal-containing poly(vinyl pyrrolidone) microfibers
Eva Enz, Ute Baumeister, Jan Lagerwall
Beilstein J. Org. Chem. 5, 58, doi:10.3762/bjoc.5.58 (2009), themed issue on ‘Progress in Liquid crystal Chemistry’.
Depending on the exact choice of liquid crystal and its properties, these composite fibers have potential for different types of functional textile. The cholesteric liquid crystal-containing fibers shown above could for instance be used for creating sensors that can be incorporated into clothing. It would require no power supply and it would offer an extremely simple color-change read-out mechanism, observable directly by eye. With other phases the fibers might be used in photovoltaics or other types of energy conversion. Our current thrusts in this research activity aim to explore these opportunities.
General references
[1] A. Greiner, and J.H. Wendorff, ‘Electrospinning: A fascinating method for the preparation of ultrathin fibres’, Angew. Chem. (Int. Ed.), 46, 30, pp. 5670-5703 (2007) ; D.H. Reneker, and A.L. Yarin, ‘Electrospinning jets and polymer nanofibers’, Polymer, 49, 10, pp. 2387-2425 (2008) ; D. Li, and Y. Xia, ‘Electrospinning of Nanofibers: Reinventing the Wheel?’, Adv. Mater., 16, 14, pp. 1151-1170 (2004)
[2] J. McCann, D. Li, and Y. Xia, ‘Electrospinning of nanofibers with core-sheath, hollow, or porous structures’, J. Mater. Chem., 15, 7, pp. 735-738 (2005)

Three most recent publications
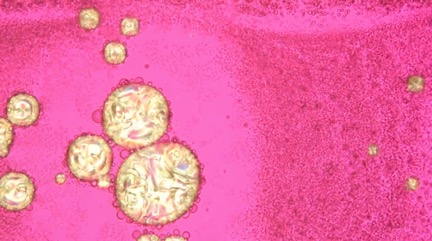
Isotropic-isotropic phase separation and spinodal decomposition in liquid crystal-solvent mixtures, Catherine G. Reyes, Jörg Baller, Takeaki Araki and Jan P. F. Lagerwall , soft matter, 2019,15, 6044-6054
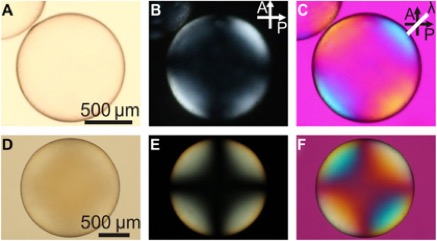
Liquid crystal elastomer shell actuators with negative order parameter, V. S. R. Jampani, R. H. Volpe, K. Reguengo de Sousa, J. Ferreira Machado, C. M. Yakacki and J. P. F. Lagerwall, Sci.adv.,DOI 10.1126/sciadv.aaw2476
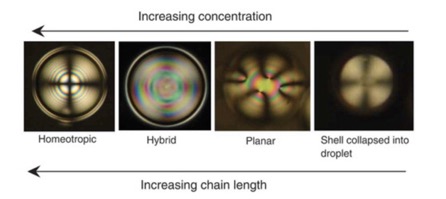
Influence of head group and chain length of surfactants using for stabilising liquid crystal shells,
Anjali Sharma and J.P.F. Lagerwall,
Liquid crystals, DOI 10.1080/02678292.2018.1509391More publications can be found here.